Exploring Conversion Coatings for Machined Magnesium Alloys
Introduction: Conversion Coatings for Elektron® Finished Parts
In this article, we compare two prominent conversion coatings: SurTec 650V and Iridite NCP. Both are renowned for their effectiveness in guarding against corrosion and their compliance with regulations. However, their applications, benefits, and suitability for different environments vary, making an informed choice essential for manufacturers.
We’ll guide you through the practical considerations of availability and cost, discuss the performance of each coating under rigorous conditions, and offer tailored technical advice from Luxfer MEL Technologies, a leader in magnesium alloy solutions. Whether you’re in aerospace, automotive, or another high-demand industry, understanding these options will help you make the best decision for your specific needs. Join us as we explore the future of conversion coatings and which coating will play a big role in sustainable manufacturing. They are not standalone solutions but integral components of a broader system that includes a suitable primer and topcoat to ensure optimal protection and performance (we’ll be releasing more on that soon!).
A Comparison of Coatings for Magnesium Machined Components
Surtec 650V
SurTec 650V offers a robust, visible blue-grey to yellow iridescent finish. This coating provides excellent corrosion protection and compliance with REACH, RoHS, and WEEE standards. It’s versatile in application, suitable for immersion, spray, or wipe methods, and can also be used to repair and refresh anodised coatings before painting.
SurTec 650V is highly regarded in the aerospace industry, meeting specifications of MIL-DTL-81706 and MIL-DTL-5541F. It is supplied as a concentrated liquid and serves as an efficient, low-resistance alternative to traditional hexavalent chrome passivation processes.
Iridite NCP
Iridite NCP is a chromium-free conversion coating, suitable for both spray and immersion applications. As a response to environmental directives such as ELV, RoHS, and WEEE, it does not contain hazardous substances like lead, cadmium, chromium, mercury, or PBB/PBDE compounds. This eco-friendly process yields a protective coating that provides corrosion resistance comparable to hexavalent chromates.
The Iridite NCP coating serves as an excellent base for paints, high-performance topcoats, powder paints, lacquers, or as a base for rubber bonding, without requiring aging or curing before topcoat application. Moreover, it features a wide operating range that accommodates various immersion times without compromising the coating’s quality or corrosion resistance.

Practical Considerations: Availability and Cost
Practical factors such as cost, availability, and lead times are crucial in choosing the right conversion coating. While both products perform excellently, their commercial availability and the cost-effectiveness of implementing them into existing production lines can vary, making it essential for manufacturers to evaluate both against their specific needs. With Iridite, curing time is eliminated, enhancing availability and efficiency, and importantly, it is a chromate-free solution, aligning with environmentally-conscious manufacturing practices.

Performance in Practice
When it comes to performance, both coatings excel in creating a strong foundation for further protective layers. They have been rigorously tested in environments simulating prolonged exposure to corrosive elements, with our salt fog tests demonstrating their effectiveness in protecting the underlying magnesium alloys (see image).
Tailored Technical Advice
Luxfer MEL Technologies, a leader in magnesium alloy solutions, offers personalized technical advice to help customers choose the most suitable coating based on their specific application and environmental requirements. Their expertise ensures that each customer can optimise their coating process to reduce steps and maximise efficiency. We’d love to hear more about your applications and offer you full support throughout the process of turning magnesium materials into finished components.
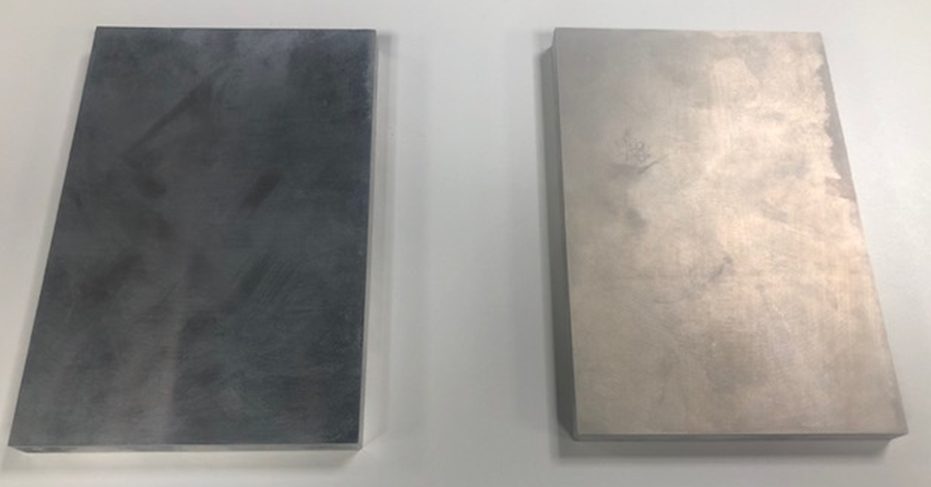
Conclusion: A Future without Chromate
As industries evolve away from chromate-based coatings in favour of more sustainable solutions, the focus shifts towards alternatives that not only meet new environmental regulations but also uphold stringent performance standards. Iridite NCP stands out as the choice, offering exceptional protection and adhesion properties without the use of chromates. For businesses aiming to adapt to stricter regulations while ensuring high product quality, prioritizing chromate-free alternatives like Iridite NCP is becoming increasingly essential.
Luxfer MEL Technologies is dedicated to supporting clients across aerospace, automotive, defense, oil & gas, and other sectors in this transition. By emphasizing solutions that reduce environmental impact without sacrificing performance.
