Magnesium vs Aluminum in Aerospace Applications
Magnesium is the Lightest Commercially Available Structural Metal
Magnesium is the lightest commercially available structural metal and is an ideal solution for weight critical applications in aerospace. It provides a lightweight alternative to Aluminium, Titanium, Steel and Carbon Fibre.
Elektron® 21 and Elektron® 43 magnesium alloys are specifically developed for higher temperature applications in the range of 150 C to 350 C. The alloys can be cast, extruded, rolled, machined, or forged.
Magnesium as an Alternative to Aluminum
For applications operating in the temperature range of 150 C to 200 C, cast Elektron® 21 and Elektron® WE43B offer a lighter alternative to the aluminum alloys such as A356 and C355. The density of magnesium is 66% of aluminum enabling significant weight savings to be achieved.
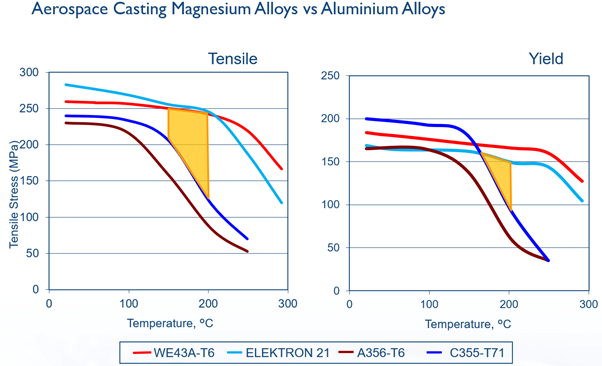
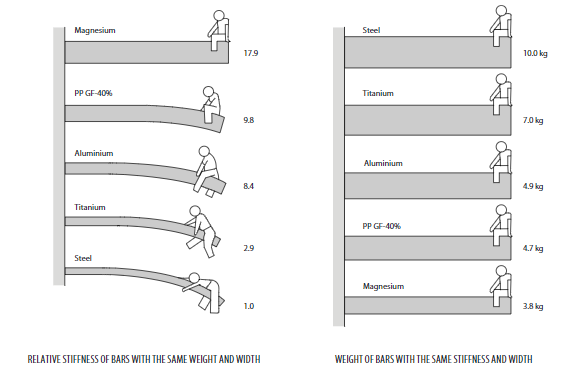
Machined Magnesium versus Aluminum
Tool ranges used during the machining of aluminum can also be used for magnesium. These give satisfactory results. However, due to the free-machining characteristics, relatively low cutting pressures and slightly lower heat capacity of magnesium, best machining practice should take tool material, tool life and tool geometry into consideration. For more information on machining magnesium, read this article.
Surface Treatment
Magnesium alloys are very stable in normal atmospheres and can be used quite freely without any particular surface protection. Elektron® 21 and Elektron® 43 both exhibit corrosion resistant behaviour similar to that of aluminum alloys. In service, magnesium alloys often have a surface treatment applied to enhance their protection. A range of surface treatments are available to suit all conditions of differing harshness.

Designing with Magnesium
It is frequently possible to take full advantage of the lower density of magnesium due to deliberate oversize by design to include features such as lugs and flanges. These considerations negate the need to proportionally stiffen magnesium components as compared with those made from alloys with a higher modulus.
A magnesium section is about 22% as stiff as steel of the same thickness but if the depth of the magnesium section is increased to twice that of the steel then the magnesium section will be 70% more rigid and yet only weigh half as much.
Similarly, on the basis of equal rigidity, a magnesium section need weigh only 75% of the aluminium one, or when compared on the basis of equal weight the magnesium will be twice as stiff.