Oil & Gas Extruded Magnesium: Not all tubes are created equal
SoluMag is a seamless extruded tube capable of higher-strength and greater resistance to deformation.
Let’s examine the extruded magnesium tube, which comes in two forms: porthole and seamless. Porthole and seamless tubes are both extruded meaning a billet of magnesium is forced through a hole in a die shaped to form the two-dimensional cross-section. Often in O&G applications, that extruded magnesium needs to have a hole down the center, which for example, is a circular tube. Porthole and seamless extrusions are different ways of forming that hollow internal section (the ID of the tube).
Porthole extruded magnesium
In porthole, metal is forced around a shape that matches the hollow section to be extruded. Physics being what it is, the tooling needs ribs to hold that shape in place, and the metal must flow around them. That separates the metal as it extrudes, so a second die forces those sections back together. That forms a longitudinal seam running the length of the extrusion.
Seamless extruded magnesium tubes
As the name suggests, seamless extruded tubes avoid this. In this process, a forming mandrel is inserted into the billet of magnesium from the rear and pushed through until it’s very close to the opening in the die. The material flows through the gap between the mandrel and die, emerging with both internal and external dimensions fixed and without any seams.
The benefits of seamless tubes
Looking at the seam through a microscope often reveals a different crystal structure to the magnesium elsewhere in the extrusion. This is a result of the grain distortion caused by the deformation and subsequent pressure that welds the separate pieces together. The extent of the difference depends on how much deformation and pressure the metal undergoes. The net effect of this distortion is to create a weaker region along the seam. In porthole tubes, welded seams create a region of weakness where the tube could rupture if subjected to high internal pressure or significant bending, as in the forces created during setting and frac pressures associated with the downhole components of a frac plug.
The importance for oil and gas
SoluMag is a seamless extruded tube capable of higher-strength and greater resistance to deformation and internal pressure during the downhole environments during a typical frac operation.
So for tubes requiring strength and consistency for downhole applications, SoluMag is the best choice for components used for frac plugs and other oil field completion equipment.
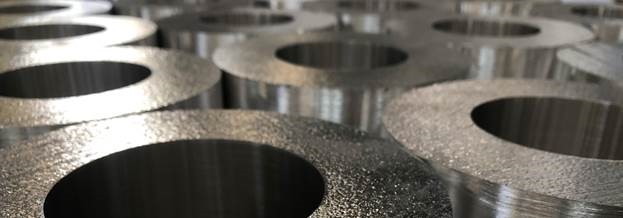